Introduction
Concrete pouring is one of the most critical phases in any construction project, whether you’re building a residential home, commercial complex, or infrastructure facility. A single mistake during this process can lead to structural failures, costly repairs, and project delays that can stretch for months.
Proper concrete pouring inspection ensures structural integrity, compliance with Indian Standards (IS) codes, and long-term durability of your construction project. This comprehensive guide covers everything from pre-pour preparations to post-construction checks, making it essential reading for construction professionals, real estate developers, homeowners planning construction, and engineering students working on project reports.
The importance of systematic concrete inspection cannot be overstated. According to industry studies, over 60% of structural failures in buildings are attributed to poor concrete quality and inadequate supervision during pouring operations. By following the inspection checklist and IS code requirements outlined in this guide, you can significantly reduce construction risks and ensure project success.

Key Methodologies & Processes
A. Pre-Pour Inspection Protocol
1. Formwork Alignment Verification The foundation of quality concrete lies in precise formwork setup. Check alignment with laser levels, ensuring tolerance remains within ±5mm as specified in IS 14687. Mark reference points every 3 meters along the formwork perimeter and verify verticality using plumb lines for wall forms.
2. Reinforcement Clear Cover Assessment Measure clear cover distances using cover meters or physical measurements. IS 456:2000 Table 16 specifies 25mm for slabs and 40mm for foundations. Install PVC spacers at 1m² intervals to maintain consistent cover throughout the pour area.
3. Shuttering Joint Inspection Test all joints for water tightness by applying cement slurry coating. Any leakage points must be sealed before concrete placement begins. Pay special attention to corners and column-beam junctions where leakage commonly occurs.
4. Embedded Items Documentation Verify placement of electrical conduits, plumbing lines, and anchor bolts against architectural and MEP drawings. Mark actual positions on as-built drawings for future reference and maintenance access.
5. Environmental Condition Assessment Monitor weather conditions and cancel pours if temperature exceeds 40°C or drops below 5°C as per IS 7861 Part 1. High winds above 25 kmph can also affect concrete placement quality.
B. Material Quality Control
6. Concrete Grade Verification Confirm grade marking (M25, M30, etc.) stamped on delivery truck chutes. Cross-check with delivery challans and maintain batch plant tickets for traceability.
7. Slump Testing Protocol Conduct slump tests following IS 1199:1959 standards. Target ranges: 75-100mm for beams and columns, 25-50mm for pavements and mass concrete. Record results every 50m³ or change in truck delivery.
8. Cube Sampling Strategy Prepare concrete cubes at frequency of 6 cubes per day or 1 set per 50m³ as per IS 456 Clause 15.2.1. Ensure proper curing and testing at 7 and 28 days for strength verification.
9. Admixture Verification Check superplasticizer dosage against laboratory trial mix designs. Overdosing can cause segregation while underdosing reduces workability. Maintain dosage within ±10% of specified amounts.
10. Temperature Monitoring Use infrared thermometers to maintain concrete temperature between 10°C to 30°C during placement. Higher temperatures accelerate setting time while lower temperatures delay strength development.
C. Pouring Process Control
11. Layer Thickness Management Limit layer thickness to maximum 450mm for vibrated concrete as per IS 7861 Part 2. Thicker layers prevent proper compaction and can cause honeycombing in lower sections.
12. Vibration Technique Standards Apply immersion vibrators for 5-15 seconds per insertion point. Maintain 450mm spacing between insertion points and avoid over-vibration which causes segregation.
13. Cold Joint Prevention Complete subsequent layers within initial setting time of 30-45 minutes. Use poker vibrators to penetrate 100mm into previously placed layer for proper bonding.
14. Pumping Operations Maintain pumping pressure between 70-100 bar for high-rise construction. Higher pressures can cause pipe blockages while lower pressures reduce pumping efficiency.
15. Bleeding Control Remove surface bleeding water using wooden floats before final finishing. Excessive bleeding indicates high water-cement ratio or inadequate cement content.
D. Post-Pour Quality Checks
16. Curing Initiation Begin curing within 2 hours for ordinary Portland cement as specified in IS 456 Clause 13.5. Delayed curing leads to surface cracking and reduced long-term strength.
17. Curing Method Selection Choose between wet hessian covering or membrane-forming compounds based on project requirements. Continuous water curing provides better results but requires more resources.
18. Formwork Removal Timeline Remove vertical formwork after 16-24 hours when concrete achieves handling strength. For slabs and beams, wait minimum 7 days or until concrete reaches 70% of design strength.
19. Surface Defect Assessment Map and document surface defects immediately after formwork removal. Honeycombing deeper than 25mm requires repair as per IS 13835 standards.
20. Early Strength Evaluation Achieve minimum 16 MPa strength before removing structural props as per IS 456 Table 11. Use rebound hammer tests for non-destructive strength assessment.
Material & Manpower Requirements
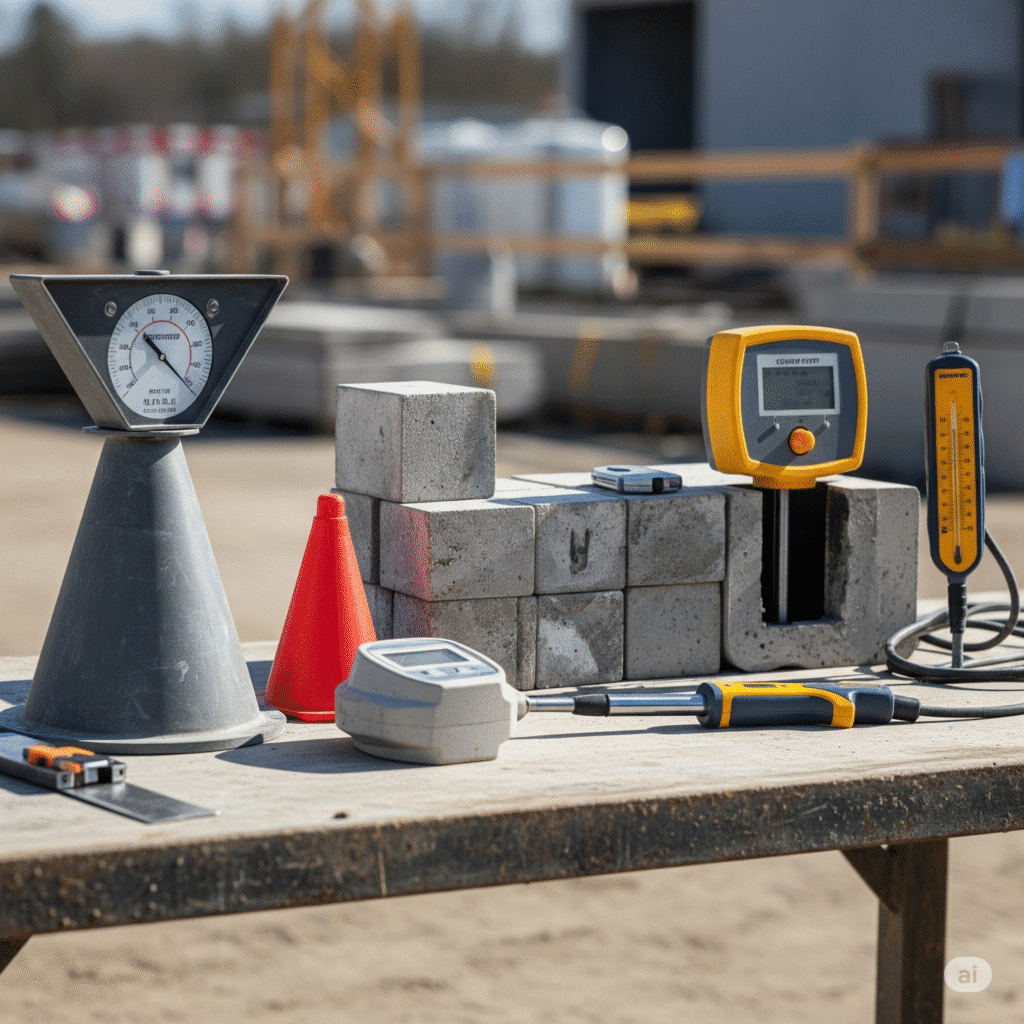
Essential Materials for Inspection
Testing Equipment:
- Slump cone and tamping rod for workability testing
- Cube molds (150mm x 150mm x 150mm) for compressive strength samples
- Cover meters for reinforcement verification
- Infrared thermometers for temperature monitoring
- Rebound hammer for non-destructive testing
Documentation Materials:
- Waterproof inspection checklists and log sheets
- Digital cameras for photographic documentation
- Measuring tapes and laser levels for dimensional checks
- Sample containers for admixture verification
Manpower Requirements
Inspection Team Structure:
- Lead Inspector: Civil engineer with minimum 5 years concrete experience
- Quality Control Officer: Testing and sampling specialist
- Documentation Assistant: Recording and reporting specialist
- Safety Officer: PPE compliance and hazard identification
Contractor Team:
- Concrete Supervisor: Experienced in mass concrete operations
- Skilled Labor: Minimum 4 workers per 100m³ pour volume
- Equipment Operators: Crane, pump, and vibrator specialists
Deliverables at Each Stage
Pre-Construction Phase
Reports and Approvals:
- Concrete mix design approval from structural consultant
- Material source approval certificates from suppliers
- Equipment calibration certificates for all testing instruments
- Weather monitoring setup and alert systems
Impact: Proper pre-construction planning reduces on-site delays by 40% and ensures regulatory compliance from project start.
Construction Phase
Daily Deliverables:
- Hourly pour progress logs with photographic evidence
- Slump test results and cube sampling records
- Non-conformance reports for any deviations from specifications
- Environmental condition monitoring data
Weekly Deliverables:
- Concrete strength test results compilation
- Material consumption analysis against estimates
- Quality trend analysis and corrective action reports
Impact: Systematic documentation during construction provides legal protection and enables quick issue resolution, reducing rework costs by up to 25%.
Post-Construction Phase
Final Deliverables:
- Comprehensive strength test report with statistical analysis
- As-built drawings with actual concrete placement details
- Maintenance manual with curing and repair recommendations
- Compliance certificate confirming IS code adherence
Impact: Complete post-construction documentation increases property value and provides warranty protection for owners and developers.
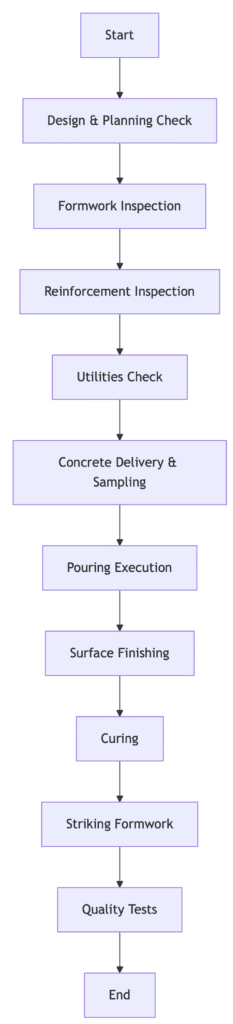
Key Checks Summary Table
Stage | Critical Checks | Standards (IS/ACI) |
---|---|---|
Formwork | Alignment, leakage, stability | IS 14687 |
Rebar | Cover, lap length, spacing | IS 456 |
Concrete | Slump, cube tests, temperature (<30°C) | IS 4926 |
Curing | Duration, method (water/membrane) | IS 7861 |
Stakeholders & Communication Matrix
Key Stakeholders
Primary Stakeholders:
- Project Owner/Developer: Overall project responsibility and funding
- Structural Consultant: Design compliance and technical approvals
- Contractor: Execution quality and timeline management
- Quality Control Agency: Independent testing and certification
Secondary Stakeholders:
- Material Suppliers: Concrete, reinforcement, and admixture providers
- Equipment Vendors: Pumps, vibrators, and testing equipment suppliers
- Regulatory Authorities: Municipal approvals and safety compliance
- Insurance Companies: Risk assessment and coverage validation
Communication Protocols
Daily Communications:
- Morning briefing with all site personnel at 8:00 AM
- Hourly progress updates during active pouring operations
- Immediate notification system for any non-conformances
- End-of-day summary report to all stakeholders
Weekly Reporting:
- Comprehensive progress report to project owner
- Technical compliance report to structural consultant
- Material consumption analysis to procurement team
- Quality trend analysis to management team
Emergency Protocols:
- 24/7 hotline for critical quality issues
- Escalation matrix with response time commitments
- Stop-work authority for safety or quality violations
Value Engineering Opportunities

Cost-Saving Techniques
Material Optimization: Replace 20-30% cement with fly ash or slag to reduce costs by ₹500-800 per m³ while maintaining strength properties. This approach also improves long-term durability and reduces heat of hydration in mass concrete.
Process Improvements: Implement self-compacting concrete (SCC) for complex geometries to eliminate vibration costs and reduce labor requirements by 30%. SCC also improves surface finish quality and reduces noise pollution.
Equipment Utilization: Optimize concrete pumping schedules to maximize equipment utilization rates from 60% to 85%, reducing rental costs and project duration.
Sustainable Alternatives
Recycled Materials:
- Use recycled aggregates for non-structural elements, reducing material costs by 15-20%
- Incorporate industrial waste materials like silica fume for high-performance concrete
- Implement water recycling systems for curing operations
Energy-Efficient Solutions:
- Solar-powered curing systems for remote construction sites
- LED lighting for night-time construction operations
- Electric concrete pumps to reduce diesel consumption and emissions
Waste Reduction:
- Just-in-time concrete delivery to minimize wastage
- Proper batching controls to achieve ±2% accuracy in material usage
- Concrete washout recycling systems for environmental compliance
Case Study: High-Rise Residential Complex

Project Overview
The Skyline Towers project in Bangalore involved pouring 15,000 m³ of concrete for a 40-story residential complex. The project faced challenges with pumping concrete to heights exceeding 120 meters while maintaining quality standards.
Challenges Faced
Technical Challenges:
- Pumping pressure limitations for high-rise construction
- Maintaining concrete workability during extended pumping times
- Coordinating multiple concrete suppliers for continuous supply
Environmental Challenges:
- Monsoon season restrictions limiting pouring windows
- Urban location constraints affecting material storage and equipment access
- Noise restrictions during night-time operations
Solutions Implemented
Technical Solutions:
- Implemented staged pumping system with intermediate pump stations at every 15 floors
- Used high-range water reducers to maintain workability for 90 minutes
- Established backup concrete supply contracts with three different plants
Process Improvements:
- Developed weather-resistant formwork systems for monsoon construction
- Created detailed logistics plan for urban construction constraints
- Implemented noise control measures including sound barriers and restricted operation hours
Results & Key Takeaways
Quantitative Results:
- Achieved 99.2% compliance with strength requirements across all test samples
- Reduced concrete wastage from industry average of 8% to 3.5%
- Completed project 2 months ahead of schedule despite weather challenges
Key Lessons Learned:
- Proactive planning for high-rise concrete placement prevents costly delays
- Investment in quality control systems pays dividends in reduced rework
- Stakeholder communication systems are crucial for complex project coordination
Risks & Mitigation Strategies
Common Construction Risks
Quality-Related Risks:
- Risk: Concrete segregation during pumping operations
- Mitigation: Use appropriate admixtures and maintain proper pumping pressures
- Monitoring: Regular slump tests and visual inspection during placement
Schedule-Related Risks:
- Risk: Weather delays affecting pouring schedules
- Mitigation: Develop flexible scheduling with weather buffer periods
- Monitoring: 7-day weather forecasting and alternative indoor work planning
Cost-Related Risks:
- Risk: Material price fluctuations affecting project budgets
- Mitigation: Long-term supply contracts with price escalation clauses
- Monitoring: Monthly market price analysis and budget variance reporting
Preventive Measures
Planning Phase:
- Conduct detailed soil investigation to prevent foundation surprises
- Develop comprehensive quality assurance plans before construction start
- Establish clear roles and responsibilities for all team members
Execution Phase:
- Implement daily quality checklists with mandatory sign-offs
- Maintain emergency contact lists for all critical suppliers and consultants
- Conduct weekly risk assessment meetings with all stakeholders
Monitoring Tools:
- Digital documentation systems for real-time quality tracking
- Automated alert systems for environmental condition changes
- Statistical process control for concrete strength trend analysis
Conclusion & Further Reading

Successful concrete pouring inspection requires systematic approach, adherence to IS codes, and continuous monitoring throughout the construction process. The key to project success lies in proactive planning, rigorous quality control, and effective stakeholder communication.
This comprehensive checklist and methodology ensure your construction project meets the highest standards while optimizing costs and timelines. Regular training of inspection teams and staying updated with latest IS code revisions will further enhance project outcomes.
Remember that concrete inspection is not just about compliance – it’s about building structures that will serve communities safely for decades to come. Investment in proper inspection procedures pays dividends in reduced maintenance costs, enhanced property values, and most importantly, structural safety.
Internal Resources:
- [Construction Project Management Best Practices]
- [IS Code Compliance Guide for Builders]
- [Quality Control Systems in Construction]
- [Sustainable Construction Materials Guide]
External References:
- Bureau of Indian Standards (IS 456:2000) – Code of Practice for Plain and Reinforced Concrete
- National Building Code of India 2016 – Concrete Construction Guidelines
- Indian Concrete Institute – Technical Publications and Research Papers
- Construction Industry Development Council – Quality Standards and Certification